NCVIEW/NCVIEW Neo/NCVIEW MC3 2021 release note
We have released the new versions of NCVIEW/NCVIEW Neo/NCVIEW MC3 2021.
Please refer to the release notes for more details.
Overview of New Functions
Cutting simulation of face milling tools (round piece inserts) is now available.
The cutting geometry is faithfully reproduced, and interference at the bottom of the tool, which has been difficult to check, can be checked in advance by simulation.
The maximum ramping angle can also be set for each tool to check whether the movement angle during machining is within the set range.
■ Face Mill Tool Registration Screen Tools can be registered from an easy-to-understand setup screen.

■ Ramping process operation check
- Detects interference at the bottom of the tool (inside part from the tip).
- Checks whether the direction of motion exceeds the set ramping angle.
- In the same way, interference at the bottom of the tool (inside the insert) is detected in helical machining.
*The interference check/ramping angle check for face milling tools is a function of NCVIEW Neo / NCVIEW MC3.
Improved Cutting Simulation Processing Speed
Cutting simulation time can be reduced by 50%-90% compared to NCVIEW2020.
■ 3-axis die machining A
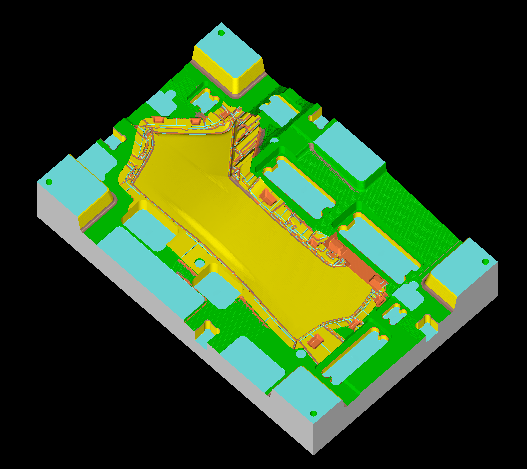
Total processing time: 122 hours
Simulation time
NCVIEW2020: 630 minutes
NCVIEW2021: 127 minutes (80% reduction)
Material dimensions: 1350 x 900 x 280
NC data: 13 million lines
■ 3-axis mold machining B
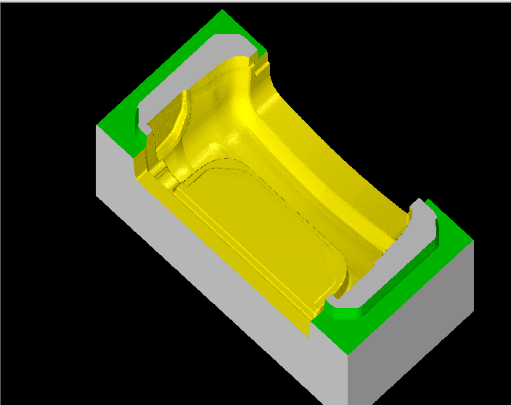
Simulation Time
NCVIEW2020: 260 sec.
NCVIEW2021: 107 sec (60% reduction)
Material dimensions: 2000 x 1000 x 850
NC data: 450,000 lines
■ Simultaneous 5-axis machining
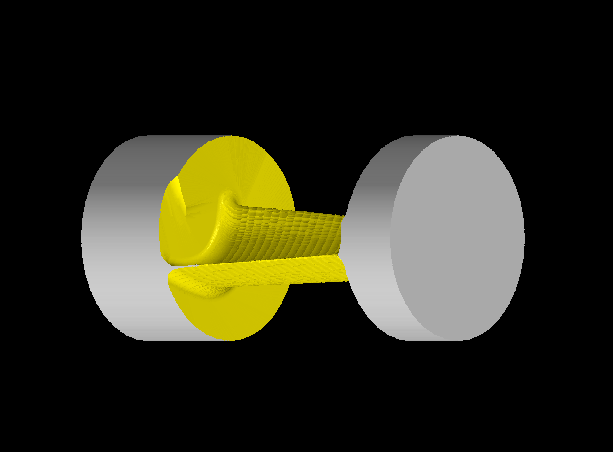
Simulation Time
NCVIEW2020: 103 sec.
NCVIEW2021: 19 sec (80% reduction)
Material dimensions: 100φ x 200
NC data: 5000 lines
■ 5-axis indexing machining
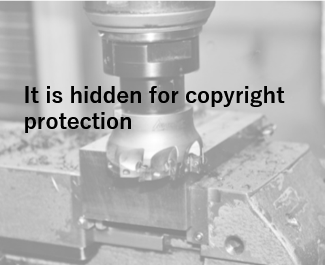
Total processing time: 60 minutes
Simulation time
NCVIEW2020: 176 sec.
NCVIEW2021: 18 sec (90% reduction)
Material dimensions: 20φ x 200
NC data: 3000 lines
*Simulation processing speed improvement is supported by NCVIEW Neo/ MC3.
OSP-related functions have been extended.
- OSP’s program call variable functionality is now supported.
TOSNUC-related functions have been extended.
- Symbols can now be specified for TOSNUC subprogram arguments
Fixed cycle-related functions have been extended.
- Cycle operation is not performed when “Q0.” is specified for cycle commands such as G83
Batch-related functions have been enhanced.
- Batch commands for setting the 2nd, 3rd, and 4th return values have been added.
Functions have been enhanced for easier use.
- Animation ON/OFF can now be set when NCVIEW is started.
Major Improvements and Corrections
- Modal group 30 processing has been corrected.
- Processing of macro expansion output when program number is a variable has been corrected. (20200207)
- Processing when a BC axis is commanded with an address other than ABC in the universal head has been modified.
- Processing of EXOFS for add-axis has been modified.
- Processing of batch report output has been modified.
- The VM display of fixed attachments (FIX_STL) has been adjusted. (202001002)
- Corrected processing of subpro call by file name. (202001006)
- The fast-forward locus display line in DXF output has been adjusted. (201912010)
- The processing of the type of tool tip endpoint control for inclined rotation axis where the coordinate system does not rotate with the table has been corrected.
- The processing of the tool template screen has been corrected.
- Incorrect curve output in tool locus DXF output has been corrected.
- The display of coordinate values in model comparison results has been adjusted.
- Incorrect numerical value output processing in tool locus DXF output has been corrected. (202004003)
- The alarm message display for OSP coordinate transformation (G137) has been adjusted.
- Processing of OSP coordinate transformation mnemonic COPY operation has been corrected. (202004004)
- Adjusted contact coordinate values when no contact is made in OSP skip.
- Corrected MULTIAXIS processing for sloped surface machining.
- Fixed cycle allowance processing for complex shapes in arc geometry has been modified.
- The processing of nose R compensation has been modified.
- The C-axis processing of the TOSNUC PX100 fixture offset has been corrected.
- The view display of horizontal slants has been adjusted.
- Processing of SIEMENS inequivalence operators has been corrected.
- Processing of cases where the end point of a compound fixed cycle is below the start point has been corrected.
- Processing of turning tool installation reversal has been corrected. (202003001)
- The processing of picks during locus filtering has been adjusted.
- The error checking process for tapped hole machining has been adjusted. (202009001)
- The hole processing report output display has been adjusted. (202008002)
- M code processing in CALLBYGM has been corrected. (201612005)
- The processing of tool tip endpoint control (when specifying the rotation axis of the work coordinate system) has been modified. (202011003)
- The processing of OSP system variables (workpiece coordinate system values) has been modified.
- Processing of G53 Non-directed Axis Move has been modified. (202010001)
- Status display in OSP cycle move cancel (G180) adjusted. (202004002)
- Adjusted the workpiece coordinate system preview display in the workpiece jig setting dialog.
- The project loading process at batch startup has been corrected. (202011007)
- The processing of the initial value of the rotation axis in the tool tip point control IJK command has been modified.
- Processing of interference detection during attachment rotation has been modified. (202009007)
- The processing of B-axis compensation in G43 compensation for turning tools has been corrected.
- Processing of VM interference when separated by more than the allowable amount has been corrected.
- The batch command CUT_COMP for tool compensation ON/OFF has been added to the help (202009006).
- The description of machine command help has been adjusted (202009004).
- Turning processing near the Z-axis has been corrected.
List of supported support receipt numbers
201612005, 201912004, 201912010, 202001002, 202002007, 202003001, 202003005, 202003006, 202004002, 202004003, 202004004, 202006004, 202004004, 202008002, 202009001, 202009004, 202009006, 202009007, 202010001, 202011007, 202101002
operating environment
OS | < NCVIEW / NCVIEW Neo 32-bit version > Windows 10 / Windows 10 64bit Windows 8.1 / Windows 8.1 64bit *Operates in 32-bit mode even when installed on a 64-bit OS. < NCVIEW Neo 64-bit version / NCVIEW MC3 > Windows 10 64bit Windows 8.1 64bit |
Memory | 16GB or more (64-bit) 2GB or more (32-bit) |
CPU | Intel Core i7 |
Graphics | NVIDIA |
Monitor | 1920 x 1080 |