NCVIEW/NCVIEW Neo 2017 release note
We have released the new versions of NCVIEW/NCVIEW Neo/NCVIEW MC3 2017.
Please refer to the release notes for more details.
Overview of New Functions
Tool locus drawing setting functionality has been revamped.
Tool loci displayed in the view can be filtered by tool number or workpiece coordinate system. Only the tool paths you want to see can be displayed instantly with simple operations.
- You can filter by
- Tool number
- Workpiece coordinate system
- Plane
- Feed mode
- Compensation mode
- Movement
- Multiple filtering items can be selected
- Filtering items can be set per view
- Tool and workpiece coordinate system items in the tree can be displayed only if simulation has already been run
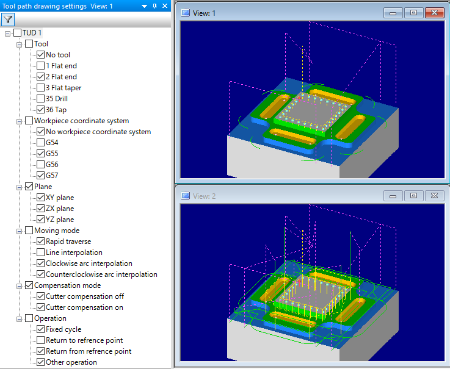
STEP file input function added
STEP files (.stp, .step) can now be input. More accurate models are input by manipulating tolerances and angles.
It can be used for the following functions
- Shape definition of attachments
- Shape definition of VM components
- [STL Operation/STEP Read] dialog
- Preview display
- Load STEP format and save it in STL format
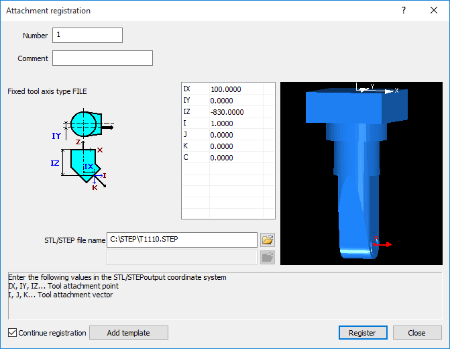
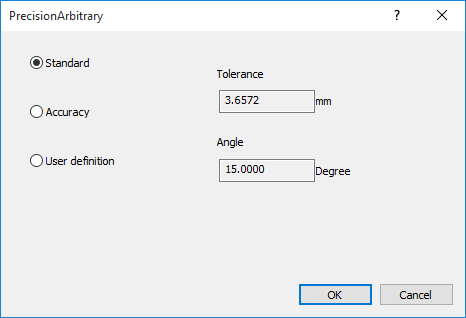
Combination holders are added
This holder type is defined by combining holders. It can be easily defined by selecting from the list of defined holders and arranging them in a row.
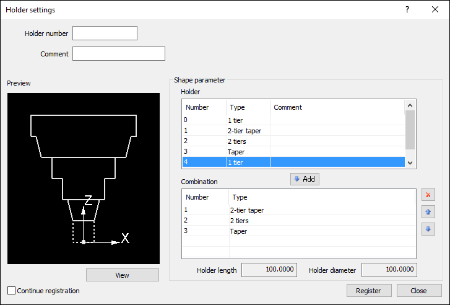
Updated to VmManager ver 1.2
- Added component placement functionality.
Components can be placed without entering numerical values with a mouse pick.
- STEP files are now supported.
STEP files can be used for component shapes.
- Drag & Drop of MSFX files is now supported.
MSFX files can be loaded by dragging and dropping them into the VmManager shortcut and window.
Time display method can now be selected
The time display method for process charts, cutting history reports, and status displays can be selected as desired.
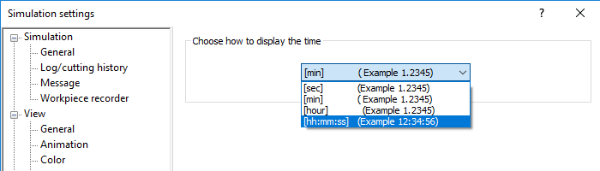
Work cross section can now be displayed on the VM screen.
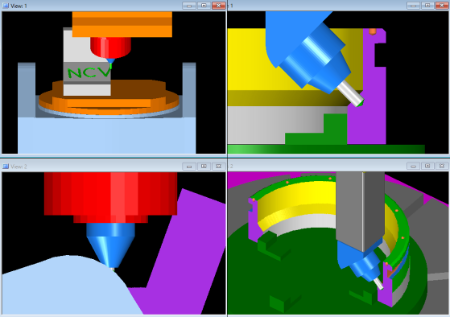
TOOLwatch can now display locus cross sections.
Drill blade length can now be entered.
Tool diameter, tip angle, and cutting edge length are automatically calculated according to the following definitions.
- When a blade length is entered, the tip angle is automatically calculated without changing the tool diameter.
- When a tip angle is entered, the tool diameter remains the same and the blade length is automatically calculated.
- When a tool diameter is entered, the tip angle remains the same and the blade length is automatically calculated.
The workpiece coordinate system can now be set in the workpiece jig setting dialog.
The work coordinate system origin can be set while checking the work coordinate system origin in the preview.
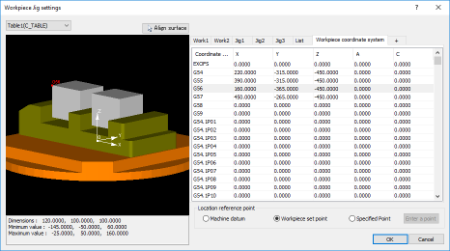
HEIDENHAIN tool diameter compensation is now supported.
HEIDENHAIN CYCLE DEF 19 (machining plane) is now supported.
FANUC 16, 18, and 30 series turning single fixed cycles (G90, G92, G94) are now supported.
The workpiece coordinate system can now be selected for model comparison positioning.
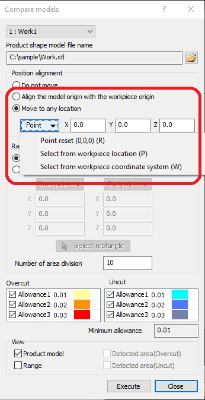
C phase can now be specified in the attachment fixed FILE (fixed file).
Expressions can now be entered for axes, workpiece coordinate system, and rotary table center in machining settings.
Calculation formulas can now be entered for list items and in the [X/Y/Z] box. Entering a formula and pressing the [Enter] key displays the calculated value.
Major Improvements and Corrections
- MELDAS subpro call has been corrected (201604007).
- Behavior when editing a tool has been corrected.
- The program number display has been corrected.
- Error output when loading a project file has been corrected.
- The NC data display when a start program number is set has been modified.
- Processing of NC data containing Japanese characters has been corrected.
- The list display of tool settings and the tree display of the registration tool window have been modified.
- The PLANE SPATIAL of HEIDENHAIN has been corrected.
- The “Spindle not rotating” message output has been adjusted.
- The behavior when 2D coordinate transformation is commanded during tip point control in OSP has been corrected.
- The loading of DXF displays has been corrected.
- The loading of machine files containing full-width spaces has been corrected.
- Model comparison display has been corrected
- Workpiece geometry created from swept body (SWP) files has been corrected (201605006)
- Model comparisons for rotary placed workpieces have been corrected.
- Turning process has been adjusted.
- The reading of compensation from tool files has been corrected.
- The XYZ (workpiece coordinates) status display has been modified.
- Tool diameter display has been corrected.
- FANUC system variables (current position) have been corrected.
- Tool locus DXF output has been modified.
- The behavior of Heidenhain’s PLANE SPATIAL when the C-axis swivels has been corrected.
- The display of NC data containing extremely long blocks has been corrected.
- The IF directive of TOSNUC has been corrected.
- TOSNUC sub-promodal calls have been corrected.
- FANUC lathe compensation system variables have been corrected.
- Machine file loading for Siemens and HEIDENHAIN has been corrected.
- The behavior of the registration tool window has been corrected.
- The animation of arc interpolation has been adjusted.
- The pick process after conversion of old format MSF files has been corrected.
- Step out and step over in HEIDENHAIN is now possible.
- Thread cutting is now supported during the G76 FANUC composite threading cycle.
- The mouse cursor display during pick mode has been improved.
- The refresh timing of the message window toolbar has been improved.
- Ball taper tool geometry has been corrected.
- Pick accuracy of jigs, chucks, and VMs has been improved.
- The collision detection for turning I.D. tools has been improved.
- DXF file input processing has been improved.
List of supported support receipt numbers
201005005、201409009、201507003、201507007 、201509002、201603001、201603002、201603005、201604007、201604007、201605004、201605006、201605007、201606007
operating environment
OS | < NCVIEW / NCVIEW Neo 32-bit version > Windows 10 / Windows 10 64bit Windows 8.1 / Windows 8.1 64bit *Operates in 32-bit mode even when installed on a 64-bit OS. < NCVIEW Neo 64-bit version / NCVIEW MC3 > Windows 10 64bit Windows 8.1 64bit |
Memory | 16GB or more (64-bit) 2GB or more (32-bit) |
CPU | Intel Core i7 |
Graphics | NVIDIA |
Monitor | 1920 x 1080 |